The Process
Preparation: Before the powder coating application, the metal object undergoes preparation to ensure a clean and smooth surface. This typically involves cleaning the object to remove any dirt, oil, rust, or previous coatings. Depending on the condition of the surface, additional steps such as sandblasting or chemical treatments may be performed.
Powder Application: Once the surface is prepared, the dry powder is applied using a spray gun or an electrostatic spray system. The powder particles are charged with an electrostatic charge, which causes them to adhere to the grounded metal object. This electrostatic attraction ensures uniform coverage and reduces waste.
Curing: After the powder is applied, the coated object is subjected to a curing process. The object is transferred to a curing oven, where it is heated to a specific temperature, typically between 160°C and 210°C (320°F and 410°F). The heat causes the powder particles to melt, flow, and chemically react, forming a solid and durable coating. The curing time varies depending on the powder type and thickness.
Cooling: Once the curing process is complete, the coated object is allowed to cool naturally or through a controlled cooling process. Cooling ensures that the coating sets properly and achieves its final hardness and durability.
Benefits of General Galvanizing
Durability: Powder coating provides a highly durable finish that is resistant to chipping, scratching, and fading. The cured coating is tougher than conventional paint, making it suitable for objects that experience high wear and tear or exposure to harsh environments.
Attractive Finish: Powder coating offers a wide range of colors, textures, and finishes, allowing for customization and creative design options. It produces a smooth, even, and high-quality finish, enhancing the appearance of the coated object.
Environmentally Friendly: Unlike liquid paint, powder coatings do not contain volatile organic compounds (VOCs) that are harmful to the environment and human health. Powder coating is a dry process, minimizing waste, and reducing the release of pollutants into the air and water.
Cost-Effective: Powder coating is a cost-effective solution in the long run. The efficiency of the application process, along with the durability and low maintenance requirements of the coating, helps reduce overall expenses. Additionally, the absence of solvent-based materials simplifies storage, handling, and disposal.
Applications of Powder Coating
Automotive Industry: Powder coating is used on automotive parts such as wheels, bumpers, grills, and engine components. The coating provides a durable finish that withstands the rigors of the road, chemicals, and weather conditions.
Furniture and Home Decor: Many metal furniture pieces, lighting fixtures, decorative items, and appliances feature powder coating. It enhances their aesthetic appeal, provides protection against scratches and corrosion, and allows for custom color options.
Architectural Applications: Powder coating is widely used in architectural applications, including aluminum doors and windows, balustrades, handrails, and building facades. It offers long-term protection, weather resistance, and customization options.
Outdoor and Sports Equipment: Powder coating is commonly used on outdoor equipment such as playground equipment, park benches, fences,
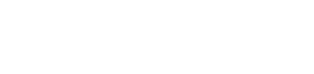
The Arkinstall Approach
We have built solid partnerships over the many years we have been trading to give us assess to shot blasting, powder coating, larger galvanizing facilities, spin galvanizers and transport companies. Arkinstall have built an enviable reputation for Hot Dip Galvanizing based on more than 120 years experience and as privately owned company, we can offer a highly personalised service tailored to meet your galvanizing requirements.
Arkinstall realise that in today’s competitive environment, companies expect the best possible service from their suppliers. Therefore, we tailor our services to suit the exacting needs of our customers, with over 50% of the goods we produce being processed and dispatched inside of 24 hours.
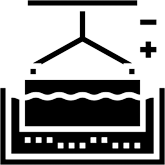
Birmingham's only
Hot Dip Galvanizer
We have an inhouse capability of up to 4m x 1.7m x 2.4m but can accommodate much larger items that can be processed through our partner facilities.
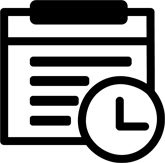
100+ years industry
Experience
As leading galvanizing experts, we pride ourselves on offering you the highest quality finished products, customer service, help and advice.
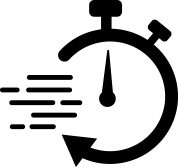
Competitive prices and
Turnaround
As the UK's leading hot dip galvanizer, offering a same day or next day service, there is no job too big or too small. Over 75% of our work is in and out within 24 hours